Tungsten Carbide Rollers Failure Prevention
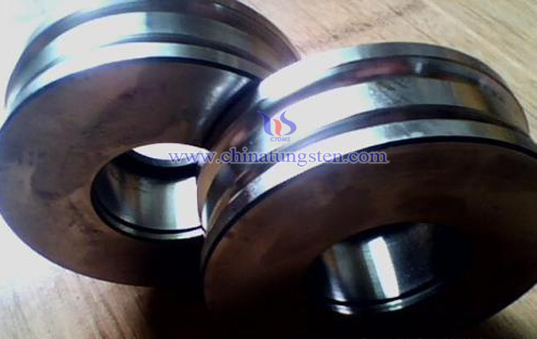
Rolling tungsten carbide rollers with good wear resistance, high temperature red hardness, thermal fatigue resistance and thermal conductivity, and high strength and other characteristics, has been widely used in high-speed wire rod, rebar, seamless steel tubes, etc. production. Domestic and foreign production of tungsten carbide rollers material mostly WC- Co, WC- Co- Ni- Cr two series, which as a binder of Co, Co - Ni - Cr content ranging 6wt% ~ 30wt%. From the use of perspective, tungsten carbide rollers have good mechanical properties, flexural strength up to 2200 MPa or more, impact toughness up (4 ~ 6) × 106 J / m2, Rockwell hardness (HRA) up to 78 ~ 90, in the high-speed wire rod rolling process, the Single too much higher than chilled cast steel or high speed steel rollers.
Pre-finishing vehicles rollers each suffered large loads such as impact and rolling force, while red hot rolled low relative velocity. Pre-finishing each frame times rollers should ensure its high toughness, strength, rigidity and thermal conductivity, followed before considering its wear resistance. Pre-finishing all vehicles rollers material design, should be used Co, Co- Ni- Cr binder content is high (greater than or equal to 25wt%) of tungsten carbide grades, requiring an average WC grain size coarse (5 μm ~ 6 μm), in order to obtain a higher impact toughness, appropriate strength and hardness.
For all vehicles rollers finishing, especially finishing the last two rollers, which suffered the load is small, but very high relative velocity of the rolled (80 m / min ~ 120 m / min). In this case, the wear resistance of the groove become the most important requirements, and must ensure the strength of the roll, the impact toughness and hardness of a reasonable match, so the content of the binder, the binder of Co / Ni content ratio and average WC grain control of particle size and other factors must have greater control different front and pre-finishing rolling roll. For pre-finishing to finishing among the various sorties rollers mill visual conditions, pass design, rolling under the pressure of the design capacity and other factors considered.
By analyzing the use of the unit rollers conditions, such as the rolling process, the unit recommended for use reasonable rollers series grades, avoiding failure modes due to improper selection error caused grades.