Tungsten Carbide Rollers Failure
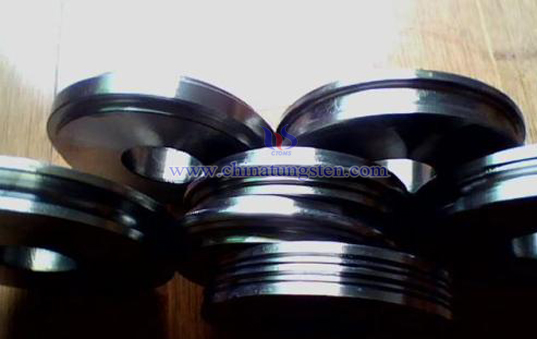
Tungsten carbide rollers for use in a variety of failure modes and their causes are analyzed to help steel companies to properly use tungsten carbide rollers at rolling speed rising, the proportion of special steel rolling significantly improve the situation, in order to improve their life and improve the quality of steel products. tungsten carbide rollers failure modes are:
1. Rollers The Normal Wear And Tear
rollers during normal use, the surface due to the effect of high-frequency alternating thermal shock and thermal fatigue cracking, which looks like a turtle shell, commonly known as cracking. When the groove face cracked it must be heavy vehicles (grinding). When cracks appear, the wear groove of generally not more than 0.1 mm, in the case of lower quality steel surface does not affect the normal rolling, but if you continue to use without grinding, Tortoise rapid expansion will eventually lead to fatal damage.
2. Rollers The Overall Fracture
rollers during use, sometimes rollers fracture phenomena, both in the form of an axial fracture, but also radial. Emergence of such phenomena caused rollers completely scrapped, seriously affected the normal operation of high-speed wire mill.
3. Rapid Wear Of The Groove
When the high-speed wire rod rolling mill rollers, excessive wear and groove, pitting or off the block, in the absence of a single slot reaches a predetermined amount can not continue to use rolling.
4. Other Failure Modes
(1) rolling groove trachoma.
(2) when overfilled or scratches rolling groove of each edge when rolling rebar, causing severe scratches interconnected cracks and other damage in the form of blocks away after the crack.
(3) steel hard spots, cooling water and solid particles of iron oxide scales scratched groove, scratches resulting cracks become the source, causing damage rollers.
(4) Since the cooling water pressure is low or the pressing means (e.g., hydraulic systems) fault rollers, so that the groove in contact with the material to be pressed too long, causing the temperature of the groove is too high, the alloy binder phase component and burnt failure.