Tungsten Carbide Rollers Production Process Control
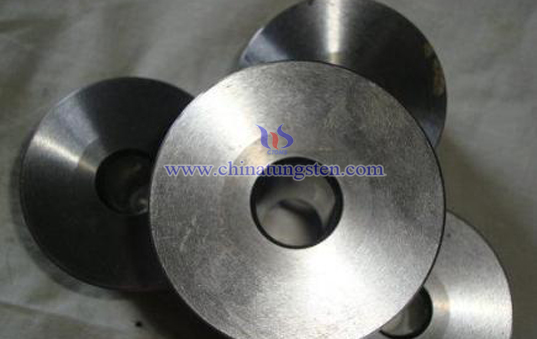
Tungsten carbide rollers produced by powder metallurgy, the key to its process control is the chemical composition of the material as well as the preparation of the mixture, pressing strictly control the molding, sintering and deep processing, such as the preparation of process parameters. Advanced manufacturing enterprises rollers through the transformation of production equipment, to promote the use of advanced technology and testing tungsten carbide manufacturing technology and strict quality control system to stabilize and improve the quality and performance of the roll. In rollers production process control should be noted:
1. The quality of the raw material WC: WC raw materials due to the use configuration of adverse effects, such as the WC grain cracks and holes. Although the cause of this defect to be further investigation, but the impact on the quality of WC alloys is rollers production must attach great importance.
2. Mixture Preparation: Preparation is the key process mixes rollers production, failure modes rollers - trachoma, is mainly produced by this procedure. The use of advanced spray drying the mixture preparation techniques, and the use of paraffin or PEG forming agent instead of behind the rubber molding agent can greatly reduce the mix of dirty, and to prevent rollers trachoma.
3. Pressing: rollers pressing process is an important rollers production molding process produces a suppression if defects such as delamination, cracking, no pressure is good and so is bound to cause a whole rollers fracture occurs when you use, do not wear, etc. failure modes. The use of large tonnage molding equipment, semi-automatic or fully automatic operation and a reasonable pressing process parameter design can greatly reduce the production of repression defects.
4. Sintering: rollers sintering decide rollers the final quality of the production process, the sintering process unreasonable cause rollers internal porosity excessive presence carburization or decarburization, greatly reducing the physical and mechanical properties of the roll, the rollers during use premature failure. The use of advanced low-pressure sintering, HIP sintering technology can greatly improve the performance of the roll.
5. Deep processing: deep processing rollers have a greater impact on the accuracy of the rollers surface quality, the larger the amount of the rollers grinding process there is a big process stress will cause the rollers for use in high-speed rolling process failure.
Faced with these difficulties in the production process control roll, you can take some measures, such as the use of advanced spray drying, large-tonnage presses pressed, low pressure sintering, ultrasonic nondestructive testing and balancing test techniques, and establish a strict quality control system in order to ensure the quality of the rollers.