Tungsten Carbide Rollers Producing Methods
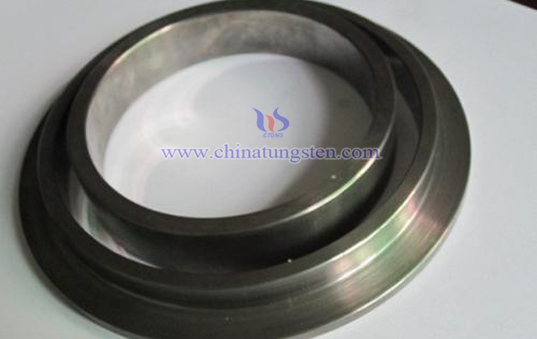
Tungsten carbide rollers have good mechanical properties, flexural strength up to 2200MPa above, the impact toughness of up to (4 ~ 6) × 106J / m2, Rockwell hardness (HRA) of up to 78 to 90. Fine tungsten carbide rollers ring material combinations, manufacturing production process is reasonable, with excellent resistance to thermal fatigue, corrosion resistance; high strength, high toughness, high thermal conductivity, high flexural strength, low wear volume, as well as good thermal rigid, life is much longer than the average roll. The method of production of tungsten carbide rollers are: three hot isostatic pressing, sintering and hot cold forming.
Cold forming sintering production process: mixing tungsten powder and WC - Grinding - granulation - dry - particle filters - pressing - prefiring - machines and molding - sintering.
Thermoforming sintering production process: hot pressing and sintering process is carried out at the same time, the product is higher than the density of hot cold products, and not easily deformed, good performance, is one of the important production of hot rollers method.
HIP production process: rollers HIP sintering is loaded into a rollers after the pressure vessel means of a high temperature, the container was evacuated, then backfilled with an inert gas, such as Ar gas. The HIP temperature is generally 13500C, this temperature is below the sintering temperature to avoid grain growth, but the temperature should be high enough so that the bonding metal can flow under gas pressure, using a pressure of approximately 1,406 kg in the HIP process / cm 2, the gas pressure within the container due to the member in all directions is balanced, thus promoting member densification. tungsten carbide using hot isostatic pressing has a density close to theoretical density can, can change the density and strength properties of the alloy roll, and better quality of the rollers material.